“Everything we do is focused on our customer requirements, reducing our impact on the environment and ensuring that we look after the health and safety of our staff.”
Why quality matters
Our advanced dispersions are the hidden component to a wide range of products where compliance, safety and enhanced performance are critical to their success.
So, quality, consistency and dependability mean a great deal.
The foundations to all aspects of quality are based on these 7 core quality management principles:
Customer focus - working with our customers to identify their challenges and objectives
Leadership - leading the way through innovation
Engagement of people - making sure that everyone is a stakeholder in our pursuit of consistent quality
Process approach - adhering to a proven tried and tested series of processes
Continuous improvement - we never stand still
Evidence - based decision making - our decisions and judgements are based on the evidence in front of us
Relationship management - adopting a collaborative approach to working with our clients.
Quality underpins every process
As an Aquaspersions customer we know you need to have the confidence that our products meet every one of their objectives, and that we can continue to supply and replenish your dispersions with the same consistent high quality - every time.
Which is why our Quality Control (QC) team plays a critical role at the heart of our business.
Their job is to make sure that the operating processes for every dispersion are followed to the letter, based on key input from our R & D and Applications team.
As part of the process, every formulation is checked against the original specification sheet for key characteristics such as viscosity and particle size. We also retain samples from the start and end of each batch to analyse consistency.
Our “tell me, show me, prove it” mantra is there to provide the internal and external rigour we demand of ourselves to ensure the integrity of our products.
Right first time approach
Time and cost pressures are, inevitably, important considerations for all our customers, so our ‘right first time’ approach aims to avoid wasting raw materials, water and other resources in refining the formulation. By getting it right first time, we can save time and be more cost effective.
Quality remains a continuing driving force behind the development of every product, which we maintain through:
Investigative-analysis
Back-end support
Product performance reports
Corrective action.
Quality accreditation
Our IS9001 standard for quality management is our benchmark evaluation framework to make sure that we meet customer expectations, along with all the legal and regulatory compliance requirements for our products and services.
Our annual quality audits are performed by ISOQAR, the external auditing body whose job it is to ensure that we rigorously adhere to our quality management standards.
.png)

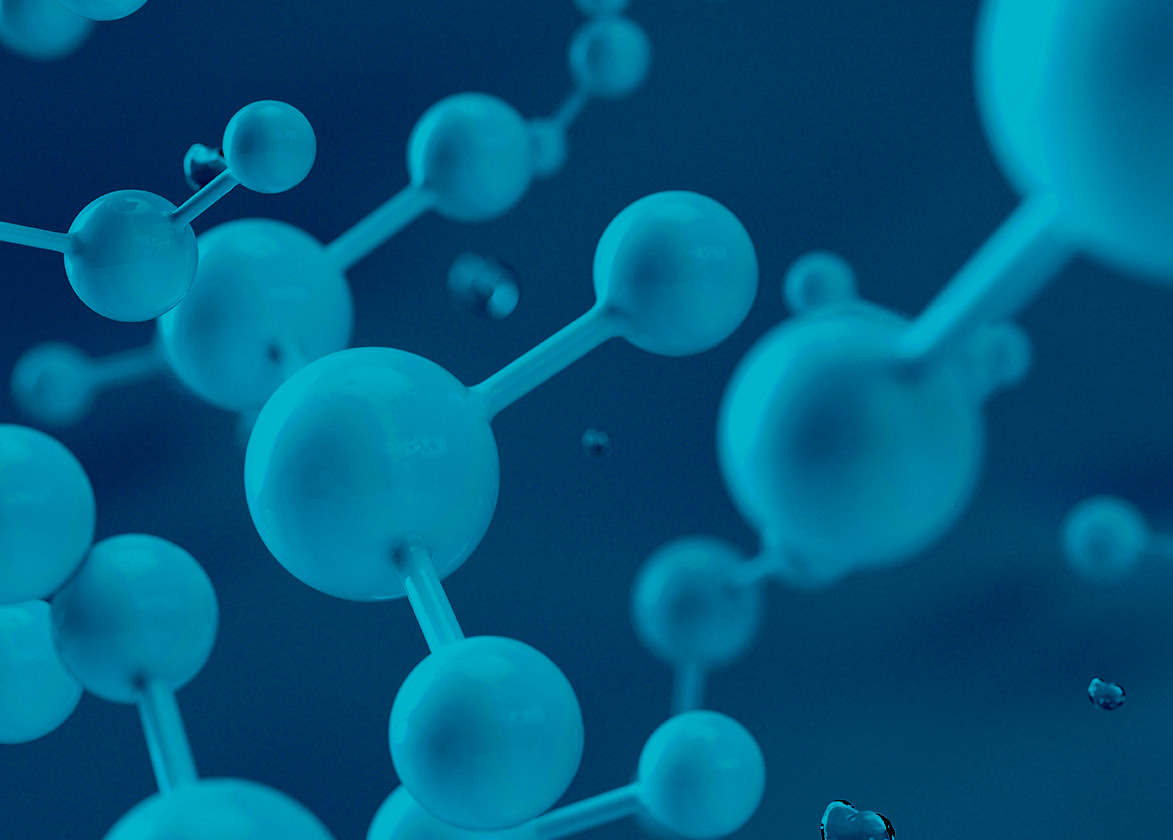
AQUAREZ®BIO Biopolymer Dispersions
Discover More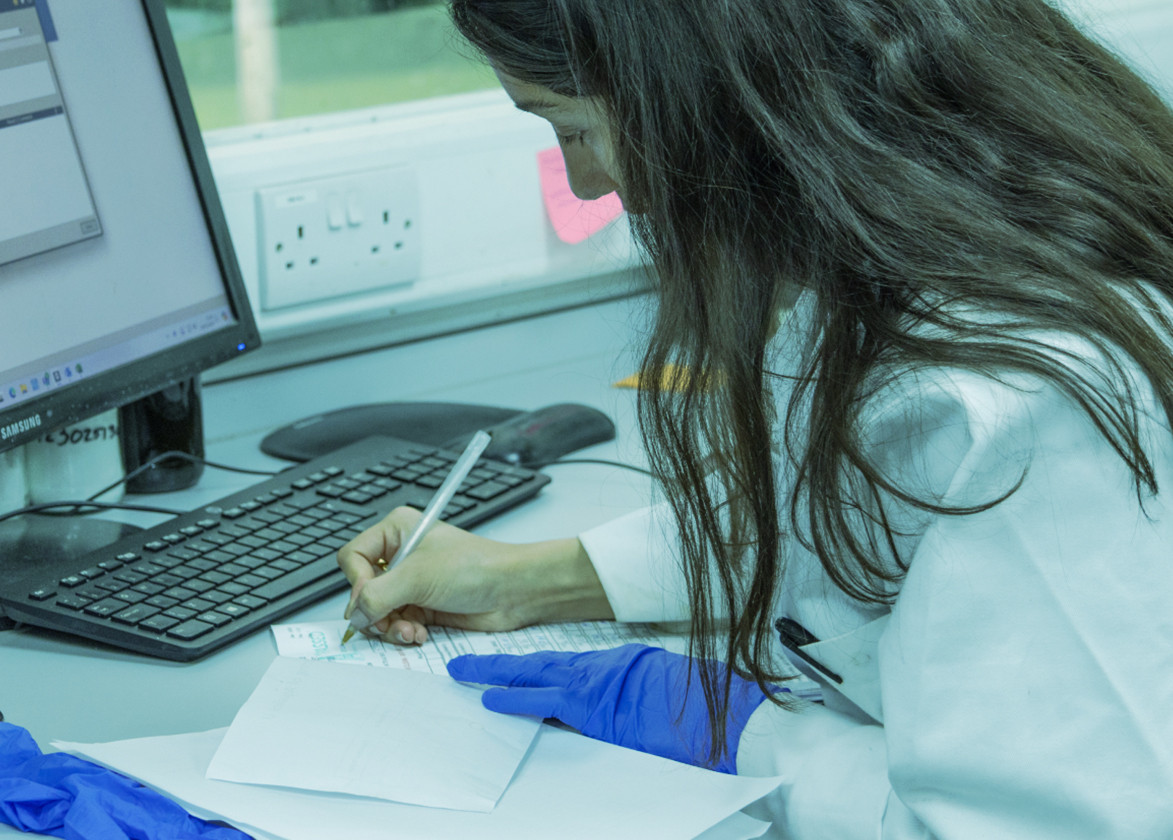
Regulatory
Discover More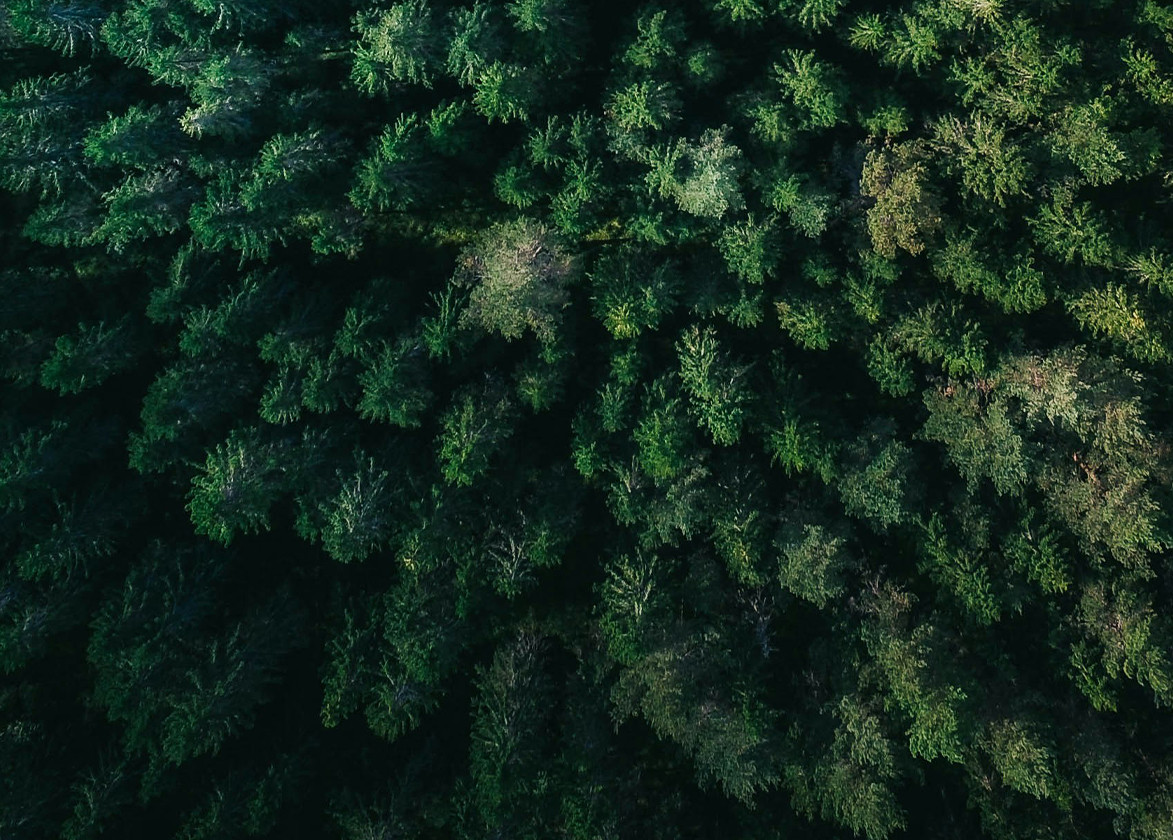
Sustainability
Discover More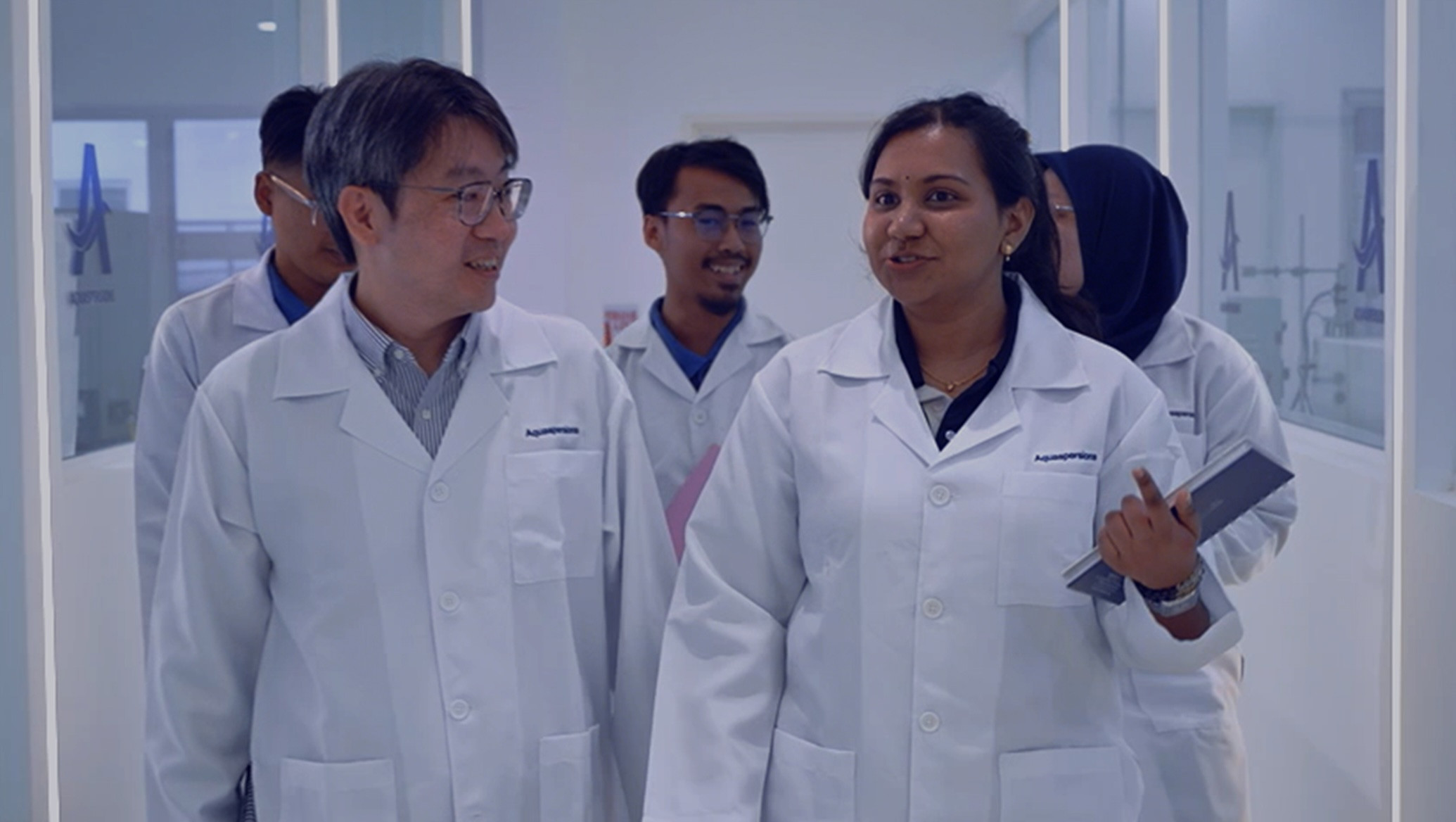